Content available at: Indonesia (Indonesian) Melayu (Malay) ไทย (Thai) Tiếng Việt (Vietnamese) Philipino
The modern world poses two major challenges for the broiler business!
- It just keeps on growing. There are already 8 billion of us.
- Chicken meat consumption is growing sustainably.
DEVELOPMENT
Within this gradual growth there are several human groups that suffer from hunger and/or malnutrition, due to the difficulty in improving the quality of the food they consume:
- Children, elderly, unemployed completely and others partially, legal and illegal refugees, homeless, indigenous, etc.
Many of them may sporadically consume and enjoy chicken meat.
This daily reality poses a great social challenge:
- Is it possible to direct the cost of a part of this process and offer it to some unprotected communities?
Fortunately, chicken continues to be consumed despite the lack of systematic campaigns to raise awareness of all the nutritional benefits of this miraculous meat!
At this point I ask myself:
Why have the leaders of these poultry associations been discreet with the purpose of disclosing all the scientifically proven nutritional benefits of chicken meat?
- It contains the highest percentage of protein – 21% – of terrestrial animal origin.
- In addition, vitamins, minerals that contribute effectively to keep us nourished and healthy.
- In Google you will find detailed benefits in the different organs and systems that make up the human being.
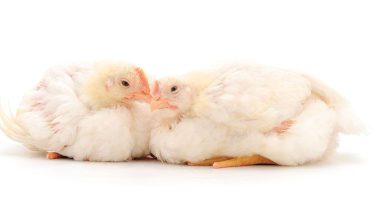
GREAT CHALLENGES, BUT ACHIEVABLE!
A mega product requires two permanent steps:
- Adjusting all waste and scrap to management parameters, broadly widely disclosed in articles published physically and digitally through the different media.
- Plan the increase of monthly broiler production, bearing in mind to create an appropriate infrastructure and operating systems so that the Saleable Product Losses (SPL), are within management parameters.
DEVELOPMENT – PRACTICAL EXPLANATION
Verification of compliance and/or reduction of the control parameters established in the preslaugether stages.
Enclosures
The poultry houses can be divided into several groups of birds, equivalent to the number of animals to be captured, caged and loaded onto trucks.
When the sheds do not have enclosures, the collection crews must build them. For this purpose, the collectors must follow the procedure established by the companies in a disciplined manner. The following are some of them:
Entrance to the booths
The catching personnel should walk slowly and quietly, so as not to cause stress to the chicks.
The collection crew must get the animals to start moving calmly to the site where the workers who will perform the trapping and caging are located.
- Achievements: Significantly decrease scratches, hemorrhages, bruises, dislocations in the thighs and/or wings, etc.
- These sufferings go in the opposite direction to the guidelines established by the Animal Welfare area.
Handling of full cages and their proper organization in trucks
They are decisive to prevent the birds from suffering any damage to their physical integrity.
Purpose: Once they reach the platform, the height of the flocks must be completed and they must be transported using specially designed carts that have a double benefit:
- In chickens, the stress caused by interrupting the tranquility that should characterize this new condition is reduced: Caged.
- The personnel decreases the fatigue curve, maintaining a stable performance.
To put into practice this dual philosophy where an environment of comfort is preserved for the protagonists in the final part of this business: the birds and their handlers.
TRANSPORTATION FROM FARMS TO SLAUGHTER PLANTS
With a few exceptions, truck drivers have traditionally been passive bystanders. They take advantage of this critical moment of loading and organizing the cargo to sleep.
This gives the impression that they have no responsibility for the physical quality of the fragile cargo they are transporting and no knowledge of the exact quantity of chickens they are moving. They limit themselves to receiving from the farm the shipment they deliver to the plant.
These three details should be monitored during transportation:
- Temperature and relative humidity inside the load where most evaporative heat is concentrated. When it goes out of the established parameters, for example: hot climates: temperature: 220C – 260C and RH: 65%, you must put the fans located behind the cabin in operation. Purpose: to reduce chicks drowning due to heat stress (DOA).
- On the road, when cornering you should slow down to about 40 km/hour to reduce the effects of the centrifugal force that moves the chickens sideways hitting their wings.
- When approaching speed bumps, the truck driver should gradually slow down to pass over them slowly. This decreases the levitation of the birds where their backs impact the top of the cages or containers.
- When they fall, they hit their breasts, causing bruises on both the back and the breast.
Drowned chickens (DOA)
The monitoring of broiler stress kills in hot climates is of utmost importance, due to the direct impact on meat yield and operating costs before reaching the plant.
In addition to the above-mentioned details, evaporative heat should be monitored during enclosures, catching and caging of the chicks from the moment when the organization of the cages with chickens starts. For this purpose, the environment around the trailers where they are being loaded should be conditioned, such as:
- Protection from sunlight, use of mobile awnings.
- Mobile fan batteries with humidifiers.
- Wet the birds as they arrange themselves on the platform.
- Conditioning of the infrastructure to be installed in the trailer to create a renewal of the interior air, entering through the aisles along the entire length of the body.
Purpose: to keep birds within comfort parameters. 220C – 260C and Relative Humidity (RH) around 65%.
Likewise, there should be other facilities in the plant designed so that the animals are calm – lacking heat stress – waiting for their turn to be processed.
If the above suggestions are followed in a disciplined manner, it is possible to reduce the traditional management parameter: 0.10% of the total number of chickens received at the slaughterhouse for the monthly process.
Some companies in Latin America are working to reduce it and stabilize it at 0.05%, e.g:
Process month: 1`000.000.000 chickens.
- Traditional DOA rate: 0.10%.
- Total, birds/month: 1,000 chickens
- New rate (NDOA): 0.05%, equivalent to only 500 birds/month.
- Annual increase: 6,000 chickens.
PROCESS PLANT
During slaughtering, a series of situations occur that affect meat quality and yield before the carcasses enter the prechiller.
The most relevant ones are listed below:
Hanging of birds on the overhead slaughter conveyor:
- The required dark environment – blue, red or green lights – must be adequate.
- Continuous air renewal to dissipate dust and dry fecal matter generated during placement of birds on the shackles, using noisy fans will affect the welfare of both personnel and animals.
- This detail affects the performance of the workers and the relaxation of the chickens.
- The correct installation and graduation of the breast massager according to the size of the birds being processed is a determining factor for them to arrive properly calm to the stunner.
- Access to the stunner should prevent birds from suffering from Pre-shock. If it occurs, intense flapping will increase and many animals will leave the water tub properly conscious.
- Consequences: hemorrhages, hematomas, wing dislocations, etc.
- The path from the exit of the water tub and the entrance to the guides of the automatic killer and/or personnel cutting the blood vessels should take 10 to 12 seconds, fulfilling the tonic and clonic stages.
- Proper slaughter and bleeding requires that the electrical variables governing stunning be properly adjusted, avoiding electrocution of chickens and ruptures of fragile thorax bones and the blood vessels that supply the muscles of this part of the body. Likewise, the bleeding time must take into account the ambient temperature and the altitude above sea level.
Purpose: Chickens must enter the scalder completely dead, after evacuating 45% to 50% of the blood. Compliance with this specific detail makes it possible to achieve the objective of carcass dry yield before falling into the prechiller.
All these data have been mentioned in previous articles.
Scalding must be carried out with total immersion of the chicks during the entire journey, appropriate water turbulence on the surface of the tanks facilitating the dilatation of the follicles and the detachment of the feathers due to protein denaturation, a sine qua non condition to achieve productive plucking.
This plucking requires that the following conditions, among others, are always met:
- Permanent supply of warm water: 34ºC to 38ºC.
- Fingers positioned with hardness according tothe part of the chickens to be in contact with.
- Complete fingers in good condition.
- The top of the plucking machines should be covered to conserve the heat that exists during feather removal.
- Plucking machines are sequentially tilted downward at the exit to increase efficiency in the removal of wing feathers that are inserted into the muscle as well as the tail feathers.
- Fingers are checked at the end of the daily shift to replace worn, split and fallen fingers. This ensures even wear and tear.
- Remember consumption parameter: 1 finger for “minimum” every 2000 chickens processed.
- Evisceration: If the established fasting and harvesting times of the birds are maintained within the established parameters and if the quality of the eviscerated chickens is affected:
- Skin stained.
- Contaminated by food.
- Lost during slaughter.
In addition, they adjust to the management indices, the accumulated losses for the different concepts must be within these reference data or be lower.
This information is updated like the well-known Guinness World Records.
Example:
- Monthly process: 1’000.000 chickens
- Average live weight: 2.3 Kg
- Total, Kilograms: 2’300.000 Kg
Extrapolated to one year, this represents an extra 49,680 Kg.
- For a company that slaughters 5 million chickens/month, it is equivalent to 248,400 Kg of additional meat.
As these new quantities are achieved, the results of having created a Micromanagement Culture, yields will rise and processing costs per kg will begin to decrease, increasing competitiveness in the marketplace.
This dreamed condition will allow offer Grade A quality products, to the most vulnerable segments of society, where to eat meat chicken, means achieving glory for eating nutritiously. This special sector of the economy will continue to increase consumption, because the companies have defined a price very accessible to their income.
The complement of the above analyzed is to determine the moment in which the poultry associations and the companies that comprise them decide prudently but irreversibly the time to increase the number of placements in the different stages of this business.
This new phase must be managed with the guidelines of the conscious companies:
“Grow friendly with the environment and humanity that will consume the best animal protein in the world!”