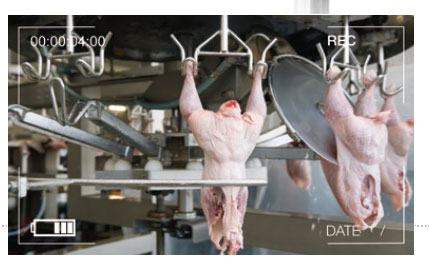
25 May 2020
Proposal for monitoring and controlling waste in plants
Content available at: Español (Spanish)For the monitoring and control of waste in processing plants, some companies have installed a camera […]
Available in other languages:
Content available at:
Español (Spanish)
For the monitoring and control of waste in processing plants, some companies have installed a camera system at strategic points in their facilities outside and inside their plants.
For this purpose, these technological watchdogs locate, among other areas, the following:
- Truck scale
- Holding shed
- Hanging live birds on the slaughter overhead carrier
- Entrance of the Scalder
- Output of the last plucker
- Hanging on the evisceration overhead conveyor
- Off the hook in the Pre-chiller
- Chiller output
- Hanging on draining overhead conveyor
- Packaging of whole chickens
- Deskinning and deboning
- Production control
- Entrance to cold rooms
- Order dispatches
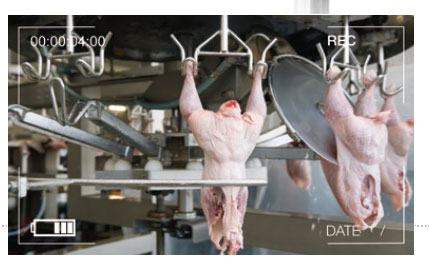
Currently, many plants have in operation a set of chambers located in different sections of the plant, cold rooms and offices, in order to evaluate the normal proceedings of all activities. For this proposal the elements to be used are:
- Strategically placed cameras in order to monitor locations where chickens fall.
- Large Screen where a minimum of 12 situations can be evaluated. A person should continuously review it.
It is suggested that cameras be directed towards:
- Stunner Entrance – Confirm that all hooks have chickens.
- Stunner Exit – Check that no chicken has been dropped after the process.
- Blood Tunnel – All hooks are full.
- Exit of the Scalder – Each hook must have a chicken
- Plucking entrance and exit – A chicken must be hung on each hook. (Photo 1)
- Automatic Evisceration – Cloaca cutter to intestinal packet extractor. After quality control inspection, some hooks are empty for one of these reasons.
- Total forfeiture
- Withdrawal of the line to locate the chickens in the reprocessing conveyor.
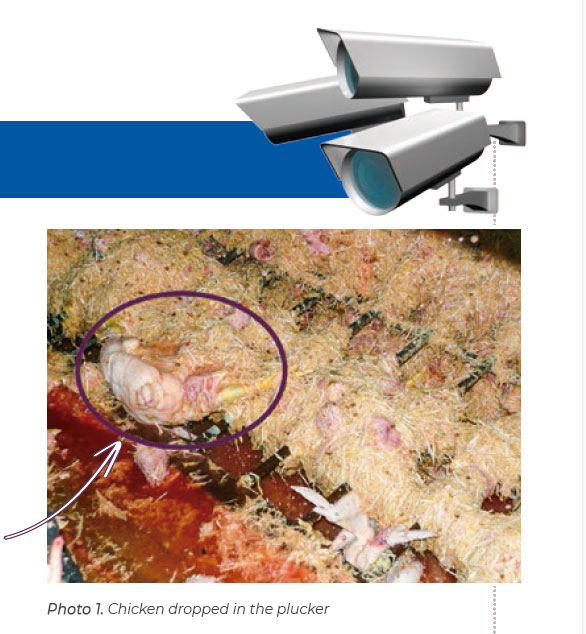
- Neck cutter
- Neck skin cutter.
- Crooper
- Washer Interior – Exterior housings
- Likewise, thegizzard processor, liver and heart cleaning and refresher station. During these operations, products accumulate in the ducts, channels, belt conveyors, etc. As they are not collected systematically, they clog and fall to the ground. (photos 2 and 3)
Packing, slicing and deboning
The carcasses are located on the overhead conveyor where they are selected for different purposes to be sent to the respective sections: Whole chicken packaging, cut-up-parts and deboning. In both situations, accumulations of products may occur that cause parts to fall on the floor.
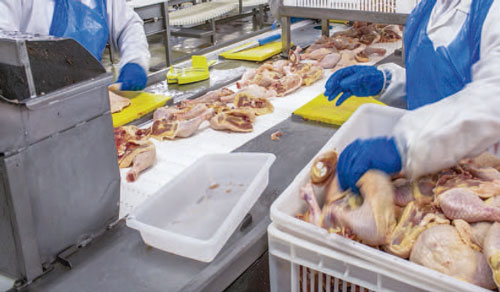
Management of the Waste Monitoring System
The person assigned to this activity must be concentrated, observing and evaluating the efficiency of each of the operations where the video cameras are located. When detecting missing birds on overhead carriers, or chickens on the bottom trays of automatic evisceration, product accumulation in the material handling infrastructure or on the floor, he must report these abnormalities to the managers of each of the sections as soon as possible , in order for them to take corrective actions. In addition, inform the Maintenance staff in case these are related to mechanical issues.
RECOMMENDATION
Use expandable hooks that guarantee the proper latching of the birds in each of the slaughter phases, regardless of their leg thickness. It is not proposed to buy new hooks. Existing ones can be redesigned.
Evisceration
Metal hooks are generally used in manual processes. These can also be redesigned so that they support the shanks, regardless of their thickness. In automatic operations, the chickens fall much less. Sometimes this is due to the fact that for various reasons the birds do not stay well positioned on the hooks and/or equipment. Manual repositioning may be a solution.
The management of these small organs is a daily challenge. Their size facilitates their accumulation, especially the infrastructure transporting them is not in optimal conditions of design or installation. Therefore, they end up on the floor. The collaboration of the personnel handling them is very important to avoid these costly losses. Even though companies do not have this simple but effective technology in place, in many plants it is observed that the products that fall to the floor represent a minimum loss of saleable products. A teamwork made in real time makes it possible. (photo 4)
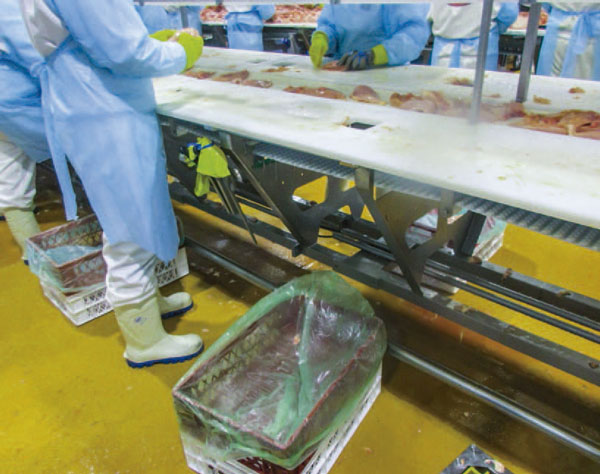
Notwithstanding what was mentioned above, plants gradually increase the number of chickens processed daily. Therefore, it is interesting to evaluate the use of Artificial Intelligence in this final part of the business. This amazing technology is already being used on farms where birds are raised and fattened. This successful real-time monitoring tool has proven to be very effective in controlling the small details during this delicate stage of production, where supervision must be carried out 24 hours, because not detecting a high risk agent and putting in order this operational or sanitary threat can affect the quality of the birds sent to the plant, as well as their respective performance.