Content available at: Indonesia (Indonesian) Melayu (Malay) ไทย (Thai) Tiếng Việt (Vietnamese) Philipino
Feathers, Fans, and Fahrenheit: The Ultimate Chick Comfort Guide!
DON’T LET YOUR CHICKS SWEAT IT OUT
We often struggle to set the minimum ventilation rate from day one and onward. Some controllers have minimum ventilation rate graphs, while others provide minimum ventilation rate levels.
- We can initially set the minimum ventilation rate with the help of the Poultry 411 app by the University of Georgia – Department of Poultry Science or simply by calculating the minimum ventilation rate as 1 CFM (cubic foot per minute) per chick.
In this process, we must consider maximum outside humidity at minimum temperature and add extra ventilation for high humidity.
- As the chicks grow, their daily water consumption increases with age, necessitating an increase in the minimum ventilation rate to match their growing needs.
The primary goal of minimum ventilation during brooding is to maintain a steady supply of fresh air for the chicks while minimizing temperature variations, drafts, and effectively managing heating costs.
This requires a careful balance of fan capacity, placement, and timing, as well as proper positioning and adjustments of air inlets. Key steps include:
- Using fans at 1 CFM per square foot and distributing fan capacity evenly between brooding and non-brooding areas.
- Ensuring proper static pressure levels when inlets are open to maintain airflow balance and limit condensation risks.
- Adjusting fan timers and inlet openings to achieve optimal air distribution based on the number of chicks, desired humidity, and ammonia levels.
- Utilizing circulation fans for even temperature distribution to support environmental uniformity throughout the brooding process.
These steps are essential for creating a controlled and efficient environment that supports chick health while minimizing energy use and potential stressors during the brooding phase.
Heating Costs: The Hidden Burden in Poultry Production
Winter is on the way. Starting in November, we will need to run more heaters while brooding chicks. In my region, most farmers use space heaters (forced air) and infrared gas brooders and the average yearly LPG gas consumption per broiler batch for brooding is around 300 kg for a poultry house that is 300 feet long, 42 feet wide, and 7.5 feet high, with insulated side curtains.
Factors Affecting Heating Costs
The heating cost of an environmentally controlled house depends on:
- Local weather
- Poultry house dimensions
- Insulation of the house
- Heater capacity
- Climate controller settings
The first three factors are fixed once the environmental control house is completed.
Heater Capacity and Climate Controller Settings
When purchasing a heater, we often ask the seller how many chicks the heater can provide heat for. This question is somewhat irrelevant.
- The heater’s capacity should be defined based on local weather conditions and the volume of the house, rather than the number of chicks.
- According to Cobb Academy’s Ventilation module, we need approximately 50 to 100 watts per cubic meter of heat (or about 5 to 10 BTUs per cubic foot).
- The purpose of heating systems is not only to maintain the required temperature but also to do so quickly.
- Therefore, it is advisable to add 20% extra heating capacity to the required heating capacity.
- Ideally, we should aim for 6 to 12 BTUs per cubic foot.
Space heaters come in different capacities, such as 73 kW, 63 kW, and 35 kW. For a poultry house measuring 300 feet by 42 feet by 7.5 feet (totaling 94,500 cubic feet), the required heater capacity would be:
94,500{cubic feet} times 12 (BTUs} = 1,134,000 {BTUs}
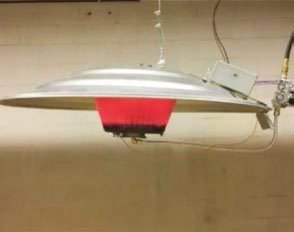
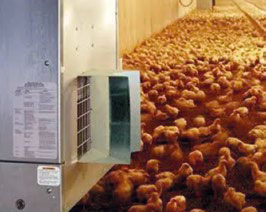
- Thus, we would need approximately five space heaters with a capacity of 245,000 BTUs each for full-house brooding.
- In a pure tunnel-ventilated house, brooding is usually done in half the house, so heater capacity can be calculated accordingly.
- In the mentioned farm, we use three space heaters with a capacity of 73 kW (LPG gasfired).
To optimize your gas bill, set an appropriate temperature differential between the required temperature and the heater’s activation temperature.
Initially, this should be as close as possible to the required temperature (e.g., 0.5 degrees). Since chicks are not fully feathered, heaters will quickly attain the required temperature and shut off.
The minimum ventilation cycle duration should be between 3 to 5 minutes.
- The Poultry411 app supports a 5-minute duty cycle.
- If the weather is too humid, a 3-minute duty cycle can be selected to prevent humidity from accumulating in the house.
- Note that this will result in more frequent fan switching.
- Additionally, keep in mind the default temperature and time delay settings in the climate controller when configuring the space heaters.
After the arrival of the chicks, the farmer is often in a state of dilemma for several days.
- He frequently expresses concern that fewer chicks are at the feeder or drinker, despite all parameters (temperature, humidity, duty cycle, and light) being set correctly.
- During this period, the retention time of the chicks at the feeder or drinkers is quite short.
In the first week, the feed consumption per chick per day ranges from 13 grams to 36 grams by the seventh day.
- This low feed intake is the reason, as we often observe that most of the chicks are resting.
- Only crop scores can provide insight into the chicks’ comfort levels.
- By day three, if a chick’s weight exceeds 100 grams, you have already made significant progress.
In poultry production, achieving optimal conditions during the brooding phase is crucial for the health and growth of chicks.
Effective minimum ventilation is essential to ensure a steady supply of fresh air while managing temperature fluctuations and humidity levels.
Properly calibrated ventilation systems help maintain a balanced environment, reducing the risks of respiratory issues and stress among chicks.
- Simultaneously, heating costs play a significant role in overall poultry management, especially during colder months.
- Understanding the dynamics of heater capacity, local climate, and house insulation is vital for optimizing energy use.
Implementing efficient heating strategies, including adequate capacity and appropriate temperature differentials, can significantly reduce operational expenses while ensuring that chicks remain comfortable and healthy.
- Moreover, attention to feeding systems is critical during the initial days post-hatch.
- Monitoring feed intake and growth rates helps identify any potential issues early on, ensuring that the chicks receive adequate nutrition to support their development.
- By focusing on crop scores and adjusting feeding strategies accordingly, farmers can better understand and enhance chick welfare.
In summary, a holistic approach that integrates minimum ventilation, efficient heating, and effective feeding systems is essential for successful brooding. By prioritizing these elements, poultry producers can foster a productive environment that supports chick health and maximizes growth potential.
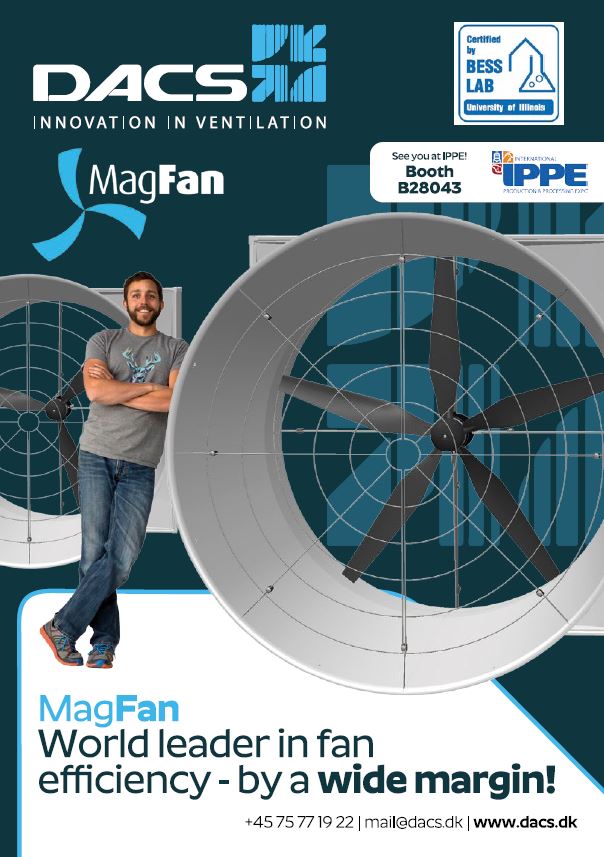