Content available at: Indonesia (Indonesian) ไทย (Thai) Tiếng Việt (Vietnamese) Philipino
Now that we understand how technologies can help producers and industry in poultry farming 4.0, Rodrigo Galli presents his vision of which technologies can and are being used to help production efficiency in traditional poultry and elevate it to farming 4.0.
In this issue he shows us how they are used in practice.
Poultry 4.0 tools play a crucial role in the efficiency of poultry production, making it possible to monitor, prevent and even predict animal performance, based on technologies such as Artificial Intelligence (AI) and Big Data.
Computer vision, for example, using deep learning, is able to monitor birds’ behavior, identifying signs of health, disease or stress, as well as evaluating the weight, volume of feed, number and egg quality.
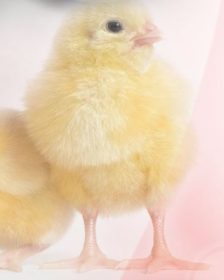
The AI also makes possible to do precise production predictions, such as the ideal time for slaughter based on marketing targets, feed consumption, egg production and bird weight.
- In addition, automation plays a fundamental role, enabling tasks such as feeding, weighing, temperature adjustment and egg collection in an automated way, which increases the efficiency of the operation.
The application of these technologies in a practical way is divided into:
- Technologies for feed mills.
- Poultry houses.
- Health.
- Management.
Let’s start with the technologies that can be applied in the feed mill.
FEED MILL PLANT
I mention three main types of NIR technologies (Near Infrared Spectroscopy) frequently used in feed mills.
- Bench (or Laboratory) NIR: This equipment is usually found in quality control laboratories. They are used for accurate analysis and detailed nutritional composition of ingredients and feed, and may some cases even analyze the impact of soybean processing and DDG. The samples are prepared and analyzed directly on the equipment, providing results in seconds.
- NIR In-line (or On-line): These systems are designed to be installed directly on the production lines feed mills and analyze the ingredients in real time, allowing immediate adjustments to formulation and dosage, guaranteeing the consistency of feed batches.
- Portable NIR: Portable NIR devices are compact and mobile that can be taken directly to suppliers of raw materials, feed mills or poultry farm installations. With internet connection, they can send data in real-time for analysis and decision making.
- We also have Process Automation, which consists of automated systems for dosing and mixing feed, reducing errors and increasing efficiency, as well as Data Traceability, which are systems for collecting and recording data in real time, making it possible to trace the origin of ingredients and control the quality.
- The data generated can still compose big data and generate analyzes that encompass data from poultry production, finding areas to improve in the productive processes.
POULTRY HOUSES
In the case of 4.0 technologies for poultry houses, several have already been implemented. Their use makes the indicators more reliable for the poultry farmer. Consequently decision making while the birds are still inside the house is more efficient and accurate. These technologies include:
- Automatic scales: Scales that monitor bird weight, making it possible through weight control to adjust feeding and identify health and welfare problems in a customized way related to weight variations.
- Environmental sensors: Humidity, temperature and air quality sensors, guaranteeing an ideal environment for the birds. They can be isolated or even associated with scales. There are already autonomous robots that move around poultry houses measuring these parameters.
- Cameras with computer vision: Cameras that monitor the birds’ behavior, calculate their weight, count the animals, as well as the eggs, and classify them (dirty, cracked, etc.). The cameras can also be used to measure the volume of feed in the silos and thus estimate feed consumption/CA.
- Autonomous robots: Robots that perform various functions, from moving the birds to stimulate consumption to identifying dead birds and collecting eggs. They can also check the litter and even collect images of droppings to identify the bird’s health status (chickenboy). Robots are not used on a large scale in Brazil, but companies and universities such as ESALQ are developing prototypes.
- Automation panels: Panels connected to sensors that automatically control systems such as ventilation, lighting and power.
- Monitoring feed in the silo
- Guided Wave Radar Sensor: This sensor uses radar waves to accurately measure the level of feed in the silo, allowing for
more efficient control of feed supplies. - Silo feed monitoring with Laser Scanners: Laser scanners scan the level of feed in the silo, providing real-time information on available feed stocks. Can also be used in grain silos.
- Monitoring feed in the silo with Load Cells: Load cells installed under the silos measure the weight of the remaining feed,
providing accurate data for replenishment planning. The most modern cells connect to the internet and send data to an app available on a cell phone or computer. - Silo feed monitoring with tension sensor: This sensor measures the tension in the silo’s suspension cable, indirectly
indicating the feed level. Based on the tension, it is possible to determine how much feed has been consumed.
- Guided Wave Radar Sensor: This sensor uses radar waves to accurately measure the level of feed in the silo, allowing for
These additional examples highlight how Poultry Farming 4.0 incorporates a wide range of monitoring technologies to ensure adequate feed supply, optimizing bird feeding and improving production efficiency.
It’s also important to keep the following question in mind: are we training employees in these technologies?
HEALTH
Preventive flock health monitoring: Digital pathogen monitoring of poultry flocks through the collection of excreta and the use of qPCR, which allows poultry producers to continuously monitor and quantify gastrointestinal (GI) pathogens quickly, accurately and reliably, with early warning of pathogen levels – allowing them to take effective preventive action, fast, accurate and reliable, in a non-invasive way.
MANAGEMENT
- Decision Support System (DSS) – The data collected generates reports and insights that help with management and decision-making. The data is unified on a single platform, allowing an overview of the entire chain, with traceability and transparency of the
business enabling the company to work with Blockchain. - Blockchain (a distributed ledger technology that allows you to track and manage information securely and efficiently):
- Improves supply chain transparency: the Blockchain can be used to improve the transparency of the poultry supply chain. This can help ensure that consumers have access to information about how poultry food has been produced.
- Dynamic planning: The data makes it possible to plan for the short and long term dynamically, optimizing processes and maximizing production.
- Through the alarms, technicians can see where there are problems and optimize their visits to the poultry houses that need support, searching for all the data stored on that batch to get to the root of the problem. This optimizes their time and the company’s resources, as well as making their work more efficient.
From these technologies Rodrigo also highlights the ability to control the farm environment intelligently. AI can regulate temperature, humidity and air quality, providing a more comfortable and productive environment for the birds.
These technologies, combined, enable more effective planning of production, optimizing processes, improving welfare and increasing overall productivity.
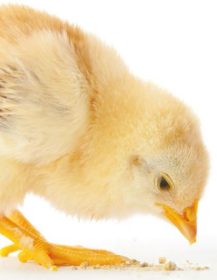
Poultry 4.0 tools go beyond monitoring and prediction. Variations in parameters outside acceptable limits, detected by sensors or data entered into cell phones, are quickly identified and generate alarms. These alarms notify the actuators, which can be automated systems, of the problem, allowing corrective action to be taken immediately.
- In addition, AI plays a central role in generating performance predictions for each flock of birds.
- These models can be adjusted according to new data, creating data, creating scenarios that guide the achievement of slaughter or egg production targets.
- This continuous cycle of analysis, adjustment and action not only increases the production efficiency, but also improves the ability to anticipate and solve problems, resulting in more effective and successful operations.